1 概况
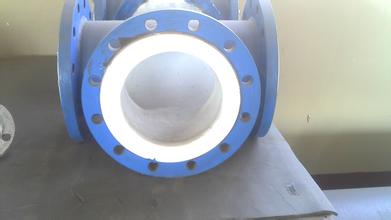
橡胶衬里是一种常用的防腐手段,它利用胶板隔离介质与金属的作用,使被保护的金属材料免遭介质的腐蚀破坏,是一项行之有效的防腐蚀技术。因橡胶具有弹性好、耐冲击、不透气、不透水、耐酸碱腐蚀且耐磨等特点,所以这项技术在化工生产等领域获得了广泛应用。橡胶衬里在我公司已应用三十多年,根据多年的生产实践,现将橡胶衬里工艺和常见的质量问题进行分析和研究,找出原因和解决措施,为有效控制、提高衬胶的质量提供一些途径,从而延长衬胶设备的使用寿命,服务于生产。
2 橡胶衬里施工工艺
橡胶有天然橡胶和合成橡胶两大类,衬里施工工艺一般有三种,即冷贴热烙法,冷贴热滚法以及热贴法,我公司以冷贴热烙法为主,其主要工序如下:
胶片下料
表面处理—→刷胶→衬贴→中间检查→硫化→成品检验
胶浆配置
2.1 表面处理
橡胶衬里的表面处理一般采用喷砂,作用有两个:一是除锈,目的是除去基体上的金属氧化物及附着物;二是打毛,目的是使基体表面具有一定的粗糙度。喷砂后基体表面呈现金属色泽,且均匀又粗糙,使橡胶与基体有很好的粘附效果。我公司采用密闭式干法喷砂,成本低,效率高,效果好,适合各种设备及管道。
表面处理的质量好坏直接影响衬里质量,要求达到Sa2.5级。表面处理后,基体表面应干净平整,无明显凹凸处,无裂纹、砂眼、气孔、毛刺、尖角等缺陷。如出现缺陷应进行修补,否则会影响衬胶质量。
2.2 胶片下料
下料应在清洁、干燥的工作台上进行,下料前要测量衬胶件尺寸,并进行排版,确定搭接方向,接缝越少越好。对几何形状简单的用计算法下料;对结构复杂不规则的异形件用放样法下料,并进行预衬;还要进行外观和漏电检查,并清理表面的线头、油污、水珠等;发现针孔、划痕、气泡、孔洞等缺陷,要进行修复;发现严重压痕、扯裂等缺陷应剪除不用。
2.3 胶浆配置
配置胶浆有人工和机械配置两种。我公司采用人工配置。以天然橡胶为例,将红胶片剪成30mm见方,放入密封桶,加入部分溶剂(120# 汽油),使胶片溶胀,再加入剩余溶剂,搅拌后密封。以后定时搅拌,直到胶块全部溶解,密封静置48 小时后使用,并在3 个月内用完。使用前应测定其稠度,一般以刷一层
胶浆可盖住金属本色又不形成厚膜为宜。如过稠,用溶剂稀释。一般刷硬质胶、碳钢表面或管道表面灌注时用稀胶(胶片∶溶剂=1∶12~15),刷软质胶、铸钢和铸铁表面用稠胶(胶片∶溶剂=1∶8~10)。
2.4 刷胶
工件喷砂后应尽快涂刷胶浆,金属表面涂刷3 遍为宜,胶片表面2 遍为宜。注入法涂刷一般注入2 遍。时间间隔以前一道表干为前提。涂刷应均匀,不得有流淌、堆积、遗漏等缺陷;涂刷时胶浆要沾饱满,反复2~3 次,不能多次反复;前后两道的涂刷方向应交错进行;涂刷用的毛刷不得混用,一把毛刷只刷一种胶浆。
2.5 衬贴
胶浆自然干燥,直到手触压稍有粘手又不起丝时,就可以贴衬了。先用垫布把刷过胶浆的胶片表面包裹起来,将垫布朝外顺次送入设备,对好位置,把端头预先粘好,边撤布边擀平,不可用力过猛或使劲拉伸胶片,否则胶片易变形、变薄或无法铺平。垫布撤出,胶片铺平后,就可压合了。压合是为了排除胶片
与金属基体或两层胶片间空气。热烙法是用120~180℃的烙铁从胶板中间向四周烙合,赶尽胶板与金属间残留空气。烙合时,烙铁温度不能太高,在胶板上停留时间不要过长,避免胶板局部温度过高而烧焦。出现气泡用针刺破,赶尽内部气体,或用针筒抽尽气体,再用刷过胶浆的胶片堵死针眼,用烙铁烙平。烙合时要重叠进行,不得漏压。
2.6 中间检查
每层胶片衬贴后,都要进行中间检查,因为硫化前查出缺陷容易修复,使衬胶质量得到保障。一般先检查外观,看是否有气泡、漏烙、接缝脱胶等现象,特别是转角、开孔部位和介质冲刷、摩擦部位; 然后用电火花检查针孔, 测试电压为5000V/mm;较后及时消除发现的缺陷,以免硫化后因前道工序原因造成起泡、开裂、针孔、搭边翘起等缺陷。
2.7 硫化
硫化是决定衬胶层物理力学性能和使用寿命的关键步骤,它是橡胶分子与硫化助剂发生化学反应的过程,它使橡胶从塑性变成弹性或硬性物体。硫化的方式有硫化釜内硫化、本体硫化、常压硫化、低压蒸汽硫化、预硫化和自然硫化等,对不同的衬胶设备、不同的胶板采用不同的硫化方式。我公司各种硫化方式都采用过,较常用的是硫化釜内硫化,其工艺简单,质量较好也较稳定。方法如下:将衬胶件装上小车,推入硫化罐,封闭罐盖;然后就通入压缩空气,直到0.3MPa;接着打开排气阀并通入蒸汽,在恒压0.3MPa 条件下置换空气;在0.3MPa 蒸汽压下保持一定时间;再通入压缩空气,在0.3MPa 恒压下置换蒸汽,使其温度下降到40℃;较后降压到零,开盖,待温度降到常温后,推出小车,硫化结束。硫化时要注意升温与降温时的温度变化,防止突然停气和各种误操作,避免硫化罐中形成真空或高温高压等事故,严格控制硫化时间防止欠硫或过硫。
2.8 成品检验
衬胶设备硫化后要进行全面质量检验,检验的主要内容有:
(1)外观检验,用目测法或用5~10 倍放大镜,检查衬胶层有无裂纹、鼓泡、接缝翘起、脱开等缺陷;用敲诊捧检查硬质胶与设备基体的贴合程度,用手指按压软质胶有无脱层。
(2)针孔检验,用电火花检测器100%检查胶层是否有针孔、裂纹等,检测电压为5000V/mm。
(3)硬度检验,用邵氏A 硬度计检查衬胶层硬度,天然硬质、半硬质胶硬度合格范围:95-98.软质胶硬度范围:50-60.
3 常见问题及原因分析
橡胶衬里在我公司已应用多年,在实践中也出现各种质量问题,下表是2005 年我公司承接的电化厂23 台电解槽盖衬胶出现质量缺陷情况统计。
从统计数据可以看出,质量问题种类虽然很多,但常见的主要有起泡、脱层、龟裂、针孔等,对衬里质量影响较大。原因分析如下:
3.1 局部起泡
局部起泡的原因较多,主要有:
(1)衬胶设备在制作过程中产生砂眼、气孔、裂纹、缩孔、锈痕、机械损伤、夹渣、焊瘤等缺陷,在喷砂后没发现或没有很好处理。
(2)涂刷胶浆后,缺陷处没有放排线或排线不合理,间隙余气无法排尽。
(3)胶浆刷得太厚或局部有堆积,溶剂不能完全挥发。
(4)硫化时操作不当或出现停电、停汽事故,造成硫化罐内压力忽高忽低或形成负压。
(5)橡胶本身存在气泡或夹层。
(6)胶浆粘上杂质或水。
(7)胶片与基体间气体没有完全赶尽。
3.2 大面积起泡
(1)环境湿度太大,温度太低。
(2)胶板存放仓库温度很低,移入衬里现场后没放置一段时间就进行下料、涂刷胶浆。
(3)胶浆中混入水分或油脂等。
(4)涂刷胶浆后干燥时间不够,未等胶浆溶剂挥发完全就进行衬贴。
3.3 脱层
(1)胶片与基体之间有水、油、粉尘等污染物。
(2)烙铁温度过低,烙合不实,气体没有排尽。
(3)环境相对湿度太大,溶剂不能完全挥发,粘接面吸附了一层水分。
(4)硫化时硫化罐内蒸汽压力不足。
(5)胶板、胶浆过期变质,胶板表面喷硫等。
(6)胶浆涂刷后干燥时间过长。
3.4 龟裂
(1)胶板过期变质;贮存温度过低,胶片变硬折裂;含硫量过高或含有杂质等。
(2)硫化时间过长,或硫化反应速度太快。
(3)机械损伤。
3.5 针孔
(1)胶片本身有针孔。
(2)施工中产生气泡,针刺后未封闭或封闭不好。
(3)衬胶设备有毛刺、尖角刺破胶板。
(4)中间检查时电火花电压过高,击穿胶板。
4 控制措施
从衬里质量问题原因分析研究中可知,影响质量的因素很多,有环境条件、设备结构、表面处理状态、材料质量、施工方法、硫化操作等,产生质量问题主要在设计、施工、材料采购管理过程中产生,而在硫化后集中反映出来。不同质量问题产生原因不同,同一质量缺陷产生原因也是多方面的。虽然产生质量问题的原因很复杂,但只要找出原因,就找出解决质量问题的措施。要控制橡胶衬里质量,针对不同原因,采取不同的措施。在设计上要考虑设备结构的合理性,结构越简单越有利于衬里;在施工中,施工人员除了有熟练衬里技术外,还要有强烈的责任心,严格按照衬里工艺和操作规程施工作业,对每道工序严格把关;在材料采购管理中,采购人员要从信誉好的正规厂商采购合格产品,同时还要进行材料复验,不让不合格的材料进入生产环节中,材料采购后要按使用说明书准确存放。
5 结果
通过以上对橡胶衬里工艺介绍及产生质量问题原因分析,我们知道要控制橡胶衬里质量,必须从设计、施工、采购等各个部门层层把关,要有全面的、科学的方法,从各方面采取措施,并不断总结、积累经验,这样才能提高橡胶衬里的质量,延长橡胶衬里设备管道的使用寿命,从而共同推动和发展橡胶衬里防腐技术,使它得到更广泛的应用。
- 上一篇:环氧玻璃鳞片如何提高建筑的寿命? 2016/10/6
- 下一篇:鳞片基长效钢结构氟碳重防腐涂层体系研究成功 2016/3/28